by Ben Feeney
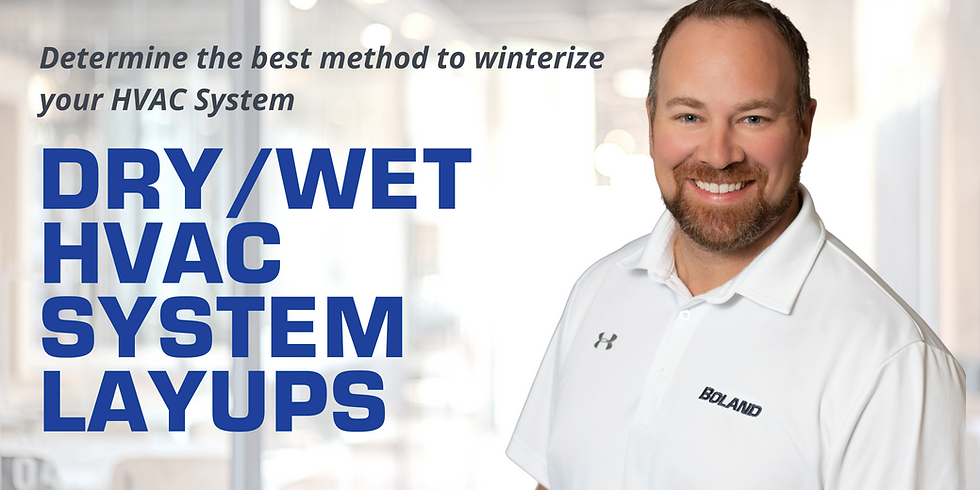
It’s that strange time of year again when temperatures fluctuate, and HVAC equipment enters a period of intermittent use. Shortly following this shoulder season is the winter shutdown.
Water treatment plays an important role in minimizing corrosion and deposit formation during both these periods. Selecting the right combination of chemical and mechanical layup methods for your facility can help save time, energy, and efficiency when spring start-up approaches.
Shoulder Season
Does your system stay off for several hours each day during the fall? The Association of Water Technologies (AWT) emphasizes the importance of running pumps for at least one hour for every six hours offline. This prevents stagnation and solids from settling, which can damage cooling equipment and piping. Often, chillers that are opened show poor results due to this period of stagnation.
Pre-Layup
Ahead of chiller layup, it’s vital to disinfect the system.
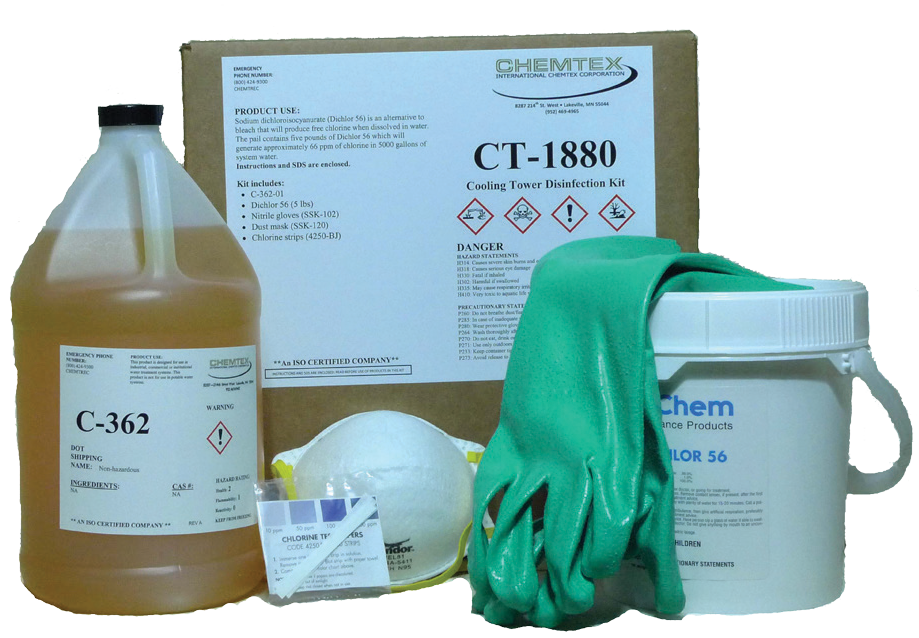
Shock treating with biocide and bio-dispersant will help kill off any biofilm that may be on the chiller tubes and other heat transfer equipment. (See BOLAND’s CT-1880 Disinfection kit).
Open chiller end bells and inspect the tubes for fouling, scale, or corrosion. Brush the tubes to remove debris before closing the equipment.
Eddy-current testing should also be performed at this time.
Dry Layup

Draining chillers is the preferred method of lay-up as suggested by ASHRAE Guideline 12. Maintaining a clean and dry environment helps prevent waterside issues like corrosion fouling and biofilm.
Leaving the chiller end bells open is preferred to allow air to circulate freely. Failure to do this allows water to pool and stagnate at the sealed ends.
Wet Layup
Many facilities require redundant equipment to be ready at a moment’s notice. In this case, the wet layup is the preferred method.
This type of layup procedure is significantly more in-depth and the following procedures should be used after inspection and tube cleaning.
Add Corrosion Inhibitor- Using a Molybdate-based corrosion inhibitor like BOLAND’s MOLYKOTE MXP or Loop Guard 505 will protect both mild steel and copper.
Add Biocide. Use a non-oxidizing biocide like BOLAND’s AA-4215 product and add it directly to the chiller to kill off any potential bacteria. This reduces the chance of biological-induced corrosion and inoculation of other harmful bacteria into the rest of the system at start-up.
If possible, set up a small recirculation pump to move the water within the chiller while it’s isolated from the rest of the system. To do this, just connect the pump to the drain lines on each end of the chiller.
Run the circulation pump for at least 1 hour for every 6 offline to prevent stagnant water.
Taking these steps each year will greatly extend equipment life and improve overall performance.
Click here to view more on our Water Treatment Solutions.
Need help? Let us know below.