Source: Chemtex
While a well-designed and executed ongoing water treatment program is crucial for maintaining a cooling tower in optimal condition, a system which has been offline requires special attention. Many building engineers are not aware that bringing a tower back online after winter lay-up or other long-term storage requires some additional specific procedures to avoid issues of corrosion and contamination.

Potential Problems Include:
Corrosion: When an empty cooling system is initially refilled with water, the unprotected metal throughout the system is vulnerable to immediate corrosion.
Particulate Matter: Dirt and debris may accumulate in the system during the lay-up period. This provides sites where under-deposit corrosion can occur, aggravating the situation.
Microbiologically Induced Corrosion or MIC: When the system is initially filled with water, it can provide an ideal environment for the growth and proliferation of bacteria and other micro-organisms.
Biofilms: Traces of oil and grease used to lubricate tower fans and other components, as well as dirt and debris, provide nutrients and serve as locations for the initial formation of biofilms. This may result in fouling of condenser tubes and other water-side surfaces, and ultimately cause MIC.
Once the system becomes imbalanced and microbiological growth and/or corrosion gain a foothold during system start-up, it's costly and time consuming to correct these conditions.
By following an appropriate protocol when starting up their cooling system after it's been dormant for as little as one or two weeks, cooling system engineers can save themselves the time and expense of restoring their system to equilibrium. They will also reduce the chance of damage to equipment.
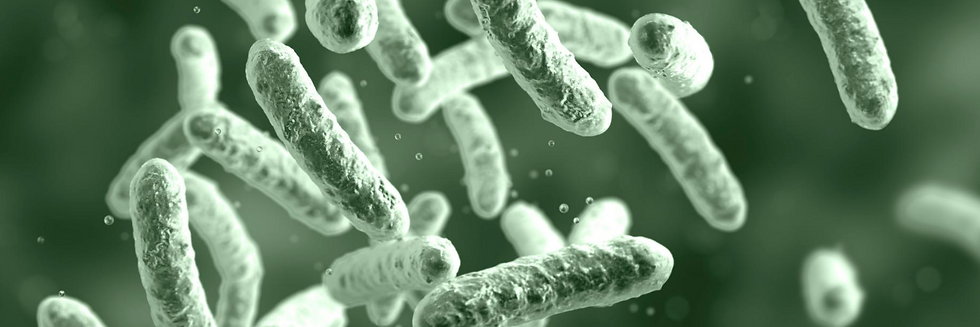
System Re-Start Protocol
Physically remove accumulated dirt and debris. Flush with fresh water to drain.
Refill system with fresh water and add twice the normal level of corrosion inhibitor; circulate for 48 hours. If possible, use a special product designed specifically for passivating the system.
If the system is operated intermittently or sporadically, make certain that biocides are added and circulated for at least two hours on a weekly basis.
Initially operate the system at lower-than-normal cycles of concentration to prevent deposition of foulants during times when system is offline. Depending on conditions, it may be advisable to add a dispersant to keep particulate matter in suspension.
If at all possible, try not to drain system piping once filled. If the system is drained, surface corrosion will begin; flushing and passivation will need to be completed again.
By investing effort in these procedures, the cooling system operator will ultimately save time, as well as operation costs.
Cooling Tower Preseason Maintenance
In addition to water treatment program concerns, this is a good time to perform routine inspections and maintenance. A little time spent now will pay big dividends by saving water, energy and chemical dollars while reducing the chance of equipment failure during peak demand.
Follow these steps to ensure efficient and trouble-free performance of your system all season long.
Prior to Filling the Tower
Check chemical feed lines for wear and damage - replace if necessary.
Inspect the tubing on the suction and discharge side of the pump. If the tubing is split where it stretches over the contact point, cut off an inch and reconnect.
Clean chemical feed pumps.
If acid is being fed, replacing lines annually is good preventive maintenance.
Running warm water through the pumps will help identify leaks and clean away any chemicals crystallized in the head.

Controller and Probes
Inspect and clean flow switch.
Check pH, ORP and conductivity probes.
Order spare replacement probes. If pH and ORP probes were not stored in holders with proper storage solution, they may not function properly.
When It’s Time to Fill the Tower
Flush the tower deck and basin to clean out any dirt, mud, iron chips or other debris. A clean tower will help prevent microbiological growth. Observe the tower hot deck during the initial circulation phase. Iron chips can catch in the tower distribution deck and prevent proper water distribution.
Chemical Feed
1. At start up, add C-364, Chemfilm MXP or other Boland recommended product to passivate system metallurgy.
2. Add an oxidizing biocide or biofilm cleaner to the system to kill any bacterial growth.
3. Add twice the normal level of corrosion inhibitor at startup. Allow the inhibitor level to cycle down to the normal operation range.
4. Circulate a minimum of 2 hours every week.
5. Make sure biocides are added weekly.
6. Additional biocide should be added at this time if regular doses are missed due to downtime.
7. Maintain bleed-off levels at the low end of the control range to help remove silt and deposits.